
Perspective of "Eleos" from above
Environmental architecture: Building materials
Starting with the drawing board, careful planning goes into the materials that will constitute an Islet. Depending on their destination, there are two categories of materials: either very durable high-tech- (structure, infrastructure), or locally replenishable low-tech materials (amenities, interiors, landscaping), but either way, they are non-toxic and recyclable (with the exception of possibly the hull of the islet, where a good choice might be ferrocement).
The Islets nurture a comfortable, care-free life, and while the Islanders are encouraged to take an active role in growing their own food and in manufacturing the amenities of their leisured life, the substrate that enables this grassroots existence is highly technical. A plethora of finely tuned, subtle technological systems enable the slice of heaven that the Floating City aims to become. Identifying where the software reaches will point out where the high-tech materials go. The computer assists or directly controls everything from the vertical movement of the Macrostructure and the Flyer Cores, to the Flyer Wings and the room aspects inside the various spaces of each Islet, in such a way that water and electricity are overall efficiently harvested and used.
Starting with the drawing board, careful planning goes into the materials that will constitute an Islet. Depending on their destination, there are two categories of materials: either very durable high-tech- (structure, infrastructure), or locally replenishable low-tech materials (amenities, interiors, landscaping), but either way, they are non-toxic and recyclable (with the exception of possibly the hull of the islet, where a good choice might be ferrocement).
The Islets nurture a comfortable, care-free life, and while the Islanders are encouraged to take an active role in growing their own food and in manufacturing the amenities of their leisured life, the substrate that enables this grassroots existence is highly technical. A plethora of finely tuned, subtle technological systems enable the slice of heaven that the Floating City aims to become. Identifying where the software reaches will point out where the high-tech materials go. The computer assists or directly controls everything from the vertical movement of the Macrostructure and the Flyer Cores, to the Flyer Wings and the room aspects inside the various spaces of each Islet, in such a way that water and electricity are overall efficiently harvested and used.
The hull: reinforced concrete
Another factor that dictates the choice of materials is the waterborne nature of the Islets. It is a salt water environment, therefore careful consideration goes into the design of anything at- and under the waterline. There are two possible choices for the hull – metal sheets (steel, aluminum) and reinforced concrete. As far as ship design goes, the hull is generally comprised of a solid hull and a system of coatings, that must handle two inherent issues: the corrosive effects of water and biofouling which in time can lead to structural damage. Concrete hulls have higher labor costs, low material costs and very low maintenance costs, compared to steel hulls. The major disadvantage of concrete ships has been the high operating costs, but given the static nature of the Islets, ferrocement edges ahead as the best choice, especially considering its most important quality – extreme durability and resilience against corrosion and biofouling, established since the 1860’s.
The structure: high-grade structural steel
The choice of materials for everything framework related is one that will best take advantage of the existing ship-building facilities and expertise. Dry docks and shipyards are already producing neighborhood sized ships, capable of accommodating 8000 people at the same time. And all this in an economic, expeditious and minutial manner. As the Islet is structurally highly complex, all materials responsible with its integrity will be of very high durability, such as high-grade steel for the framework and stainless steel as a choice for exposed surfaces to the salt air.
Surfaces: high-tech and low-tech building skins
Depending again on the specifics of the in-Islet localization, the choice for building skins may greatly vary. Initially at least, in the case of the Walkway and Flyer superstructures, glass, steel, treated wood, (for exterior surfaces), even plastics (Texlon ETFE), will be the choices de jour. Nevertheless, the Islanders are encouraged to have a hands-on approach philosophy and to make use of the various biotic and abiotic (limestone) resources that can be cultivated or harvested on site. At first the Islanders will be restricted to using the local resources for landscaping and indoors purposes (possibly stalls and pavilions on the Walkways and some green structures on the Macrostructure), but in time local wood will replace the original decks and cladding as they wear off, and ultimately, when the floating city evolves enough to accommodate its own production districts, higher tech materials will also be produced on site, such as glass, recycled steel, alternative cements and new systems that the Islander will themselves develop by trial and error. The floating city will renew its cells, as a living organism does. As its body wears off and it’s renewed with increasingly local resources, some day it will have become completely home grown.
The apartments: fiberglass laminate shells, on aluminum/ steel structural frames
The apartments have something of seaplanes design in them, present not only in their amphibious shape and hulled belly, but in the way they’re built as well. The nomad apartments must be durable and sea worthy as vessels, lightweight and rigid as planes. To achieve this, the body of the apartments is a monocoque hybrid construction, built primarily as a fiber glass and carbon fiber laminate, on an aluminum (or steel) structural frame, for stiffness and anchoring points.
Fiber glass and composites are versatile, strong, durable and affordable, and may be tooled, molded, and fabricated into virtually any shape or design, with few restrictions on color, finish, shape or size. Once the apartment sections molds have been created, parts can be easily duplicated in mass at an extremely cost effective value. The non-corrosiveness and durability of fiberglass results in lower costs for maintenance work. Additionally, the end product being lighter and stronger than alternative materials, results in additional savings in shipping and storage costs, on the way to the site. Fiberglass and composites have one of the highest strength to weight ratio available for component fabrication. Pound-for-pound, fiberglass is stronger than sheet metal or steel. Manufacturing parts from fiberglass and carbon composites builds strength directly into the finished product. Fiberglass is also highly resistant to environmental extremes, a valuable quality in marine environments. Fiberglass reinforced plastic does not rust and is highly resistant to corrosion. When exposed to extreme temperatures, salty or humid air, sun (ultraviolet light), or acidic chemicals - fiberglass, composites, and carbon fiber have excellent and lasting proven performance. The special properties of fiberglass – such as it being dielectric, chemically inert, and having superior and more desirable acoustic qualities than plastic or metal – also add to the desirability of this building material for the flying and floating apartments. Under similar conditions fiberglass and composites tend to vibrate less and remain quieter than sheet metals. And lastly, with the apartments residing most of the time high up on the wings - fiberglass and composites are structurally stable. They exhibit the least amount of expansion and contraction with heat and stress compared to plastic, metal, or wood. This means that the apartment shells will hold their shape better under severe mechanical and environmental stresses, such as the winds at that height on the superstructures, and the salty sea air and temperamental coastal weather patterns.
Structural details
• The Space Frame structural system: steel space frame, proofed against lateral movement with a ferocement staircase at the core, and further tensioned with steel cables on three sides. The black cylinder joints and their bulk must obviously be better integrated in space frame backbone of the flyer, possibly inside of an additional outer layer to the space frame system.
• Trussed walkway ribs for added rigidity.
• The hanging building core. In this scenario as vertical garden platforms.
• Administrative Pods with photovoltaic panels, at Walkways level height.
• The steel chassis structure of the apartments wings, with casings for the amphibious apartment units. 60 meters long at the tip, 11 meters wide, 4.95 meters tall
• The second floor of the apartment units, light weight shell over a steel chassis, permanently docked, adds further rigidity to the wing trussed frame by transforming it into a space frame construction.
• The fiberglass on aluminum monocoques of the apartments, being transported into the wing structure by either a floating crane or a permanent Flyer roof crane. Empty space is provided between the wings and between the apartments’ shells themselves, to mitigate the forces of the wind.
• The Cyclone Stairwells, standalone (left) and as part of the Flyer (right)
• Volumetric tensed frame construction, supports the WALKWAYS space frame
• Exterior rollercoaster lifts pulled from under the stairs
• The Space Frame structural system: steel space frame, proofed against lateral movement with a ferocement staircase at the core, and further tensioned with steel cables on three sides. The black cylinder joints and their bulk must obviously be better integrated in space frame backbone of the flyer, possibly inside of an additional outer layer to the space frame system.
• Trussed walkway ribs for added rigidity.
• The hanging building core. In this scenario as vertical garden platforms.
• Administrative Pods with photovoltaic panels, at Walkways level height.
• The steel chassis structure of the apartments wings, with casings for the amphibious apartment units. 60 meters long at the tip, 11 meters wide, 4.95 meters tall
• The second floor of the apartment units, light weight shell over a steel chassis, permanently docked, adds further rigidity to the wing trussed frame by transforming it into a space frame construction.
• The fiberglass on aluminum monocoques of the apartments, being transported into the wing structure by either a floating crane or a permanent Flyer roof crane. Empty space is provided between the wings and between the apartments’ shells themselves, to mitigate the forces of the wind.
• The Cyclone Stairwells, standalone (left) and as part of the Flyer (right)
• Volumetric tensed frame construction, supports the WALKWAYS space frame
• Exterior rollercoaster lifts pulled from under the stairs

• Elevated walkway bridging cyclone stairwells

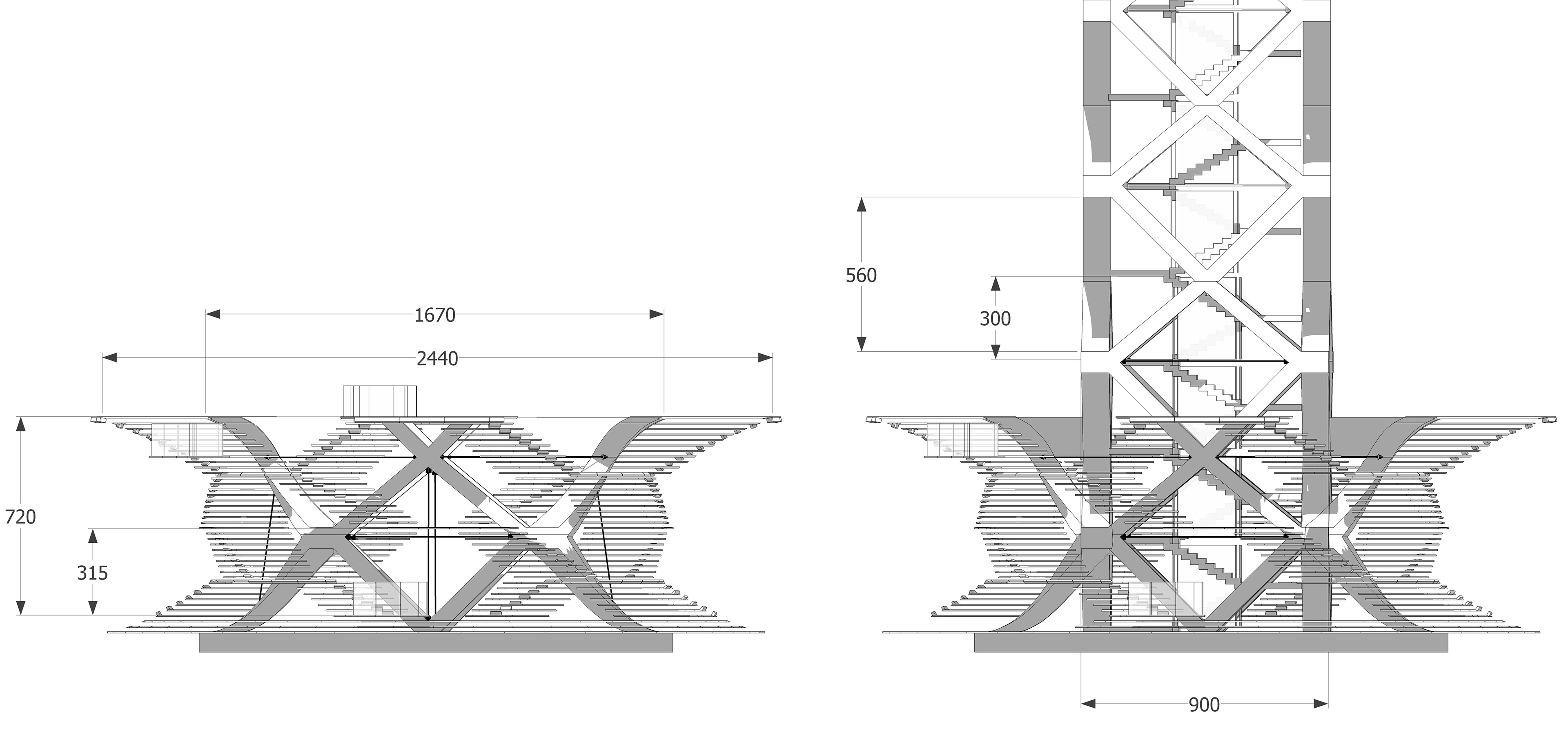

• Cyclone Stairwell

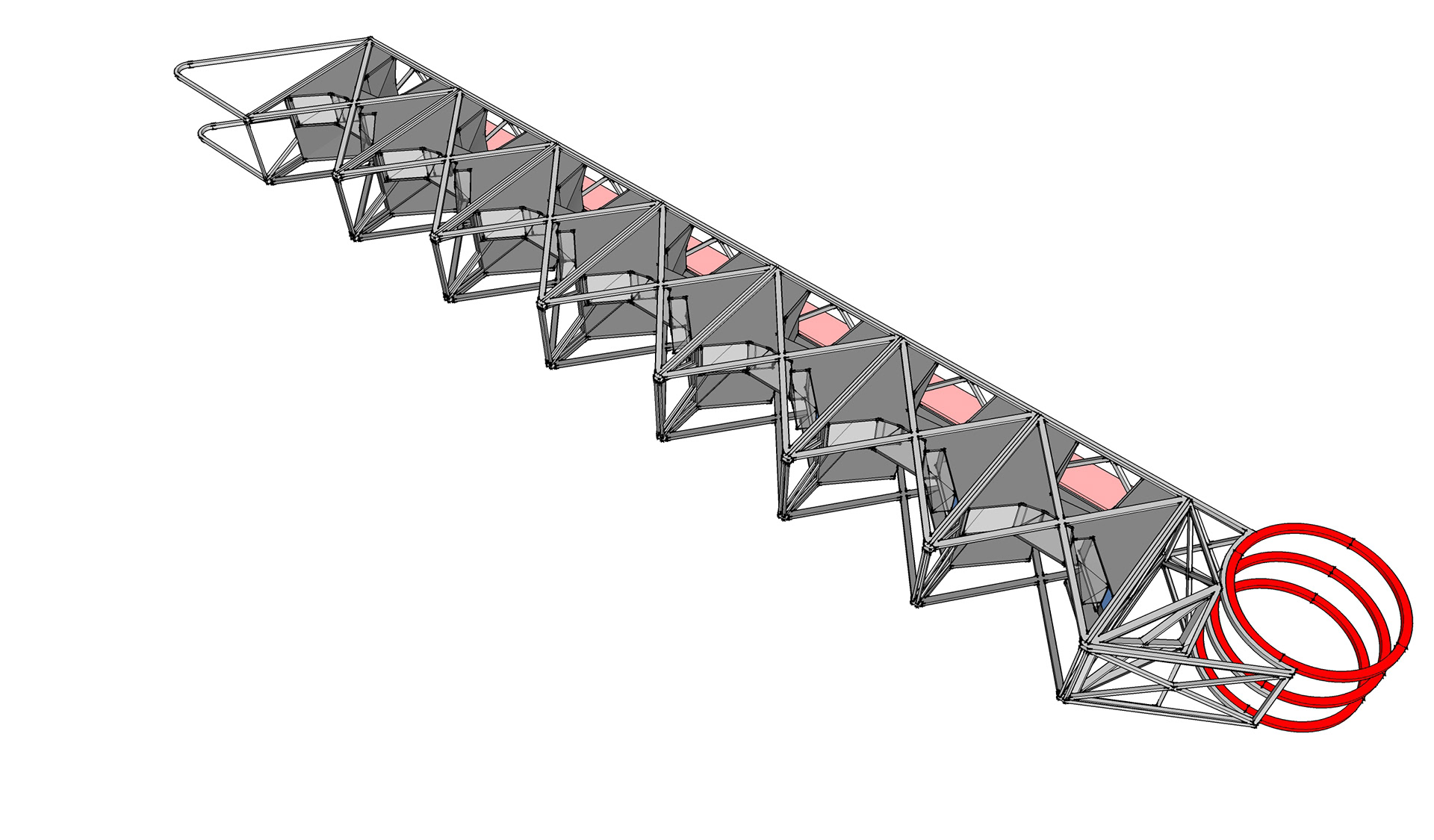
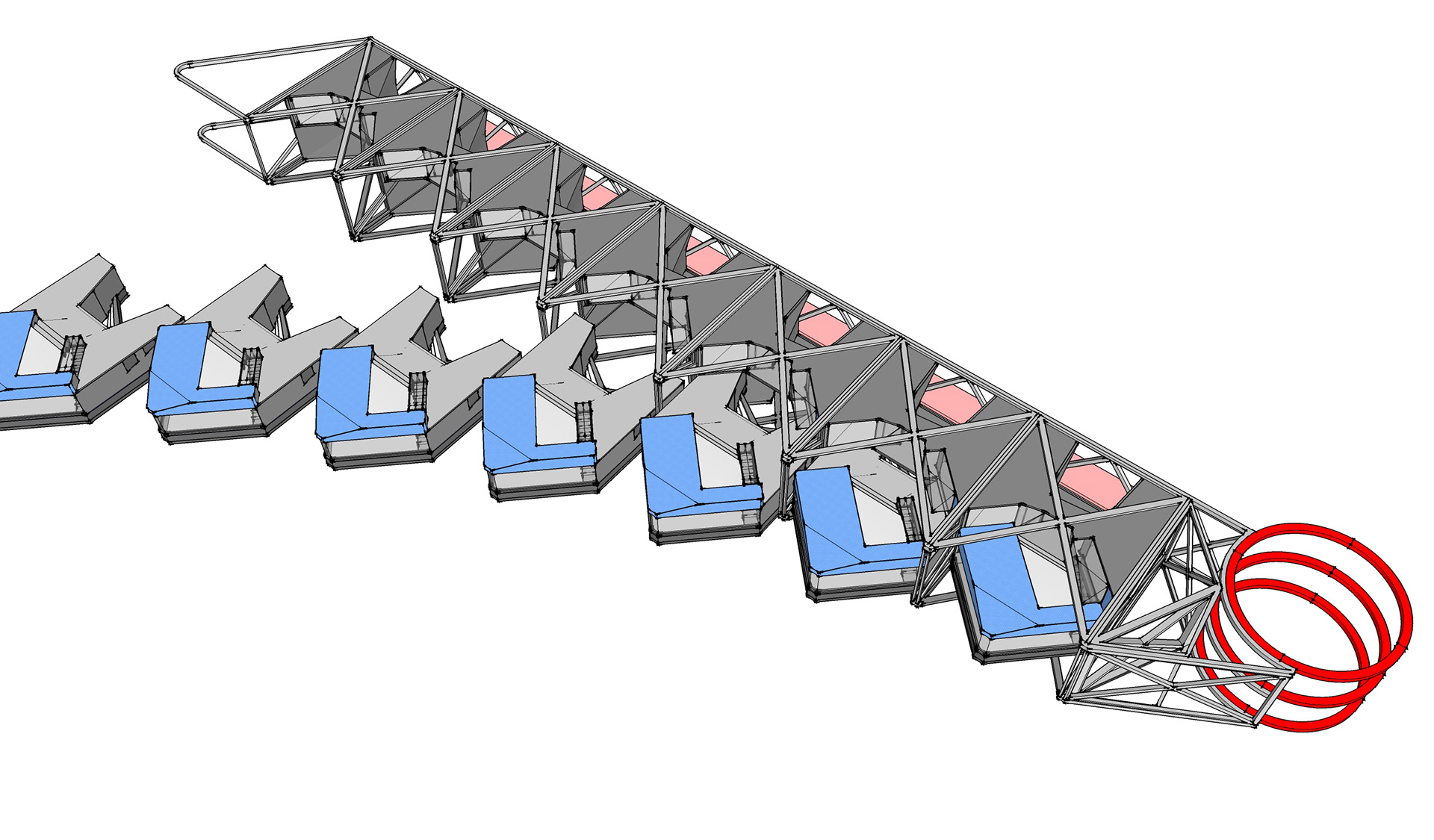
• Tower wing space frame to Apartments mobile section